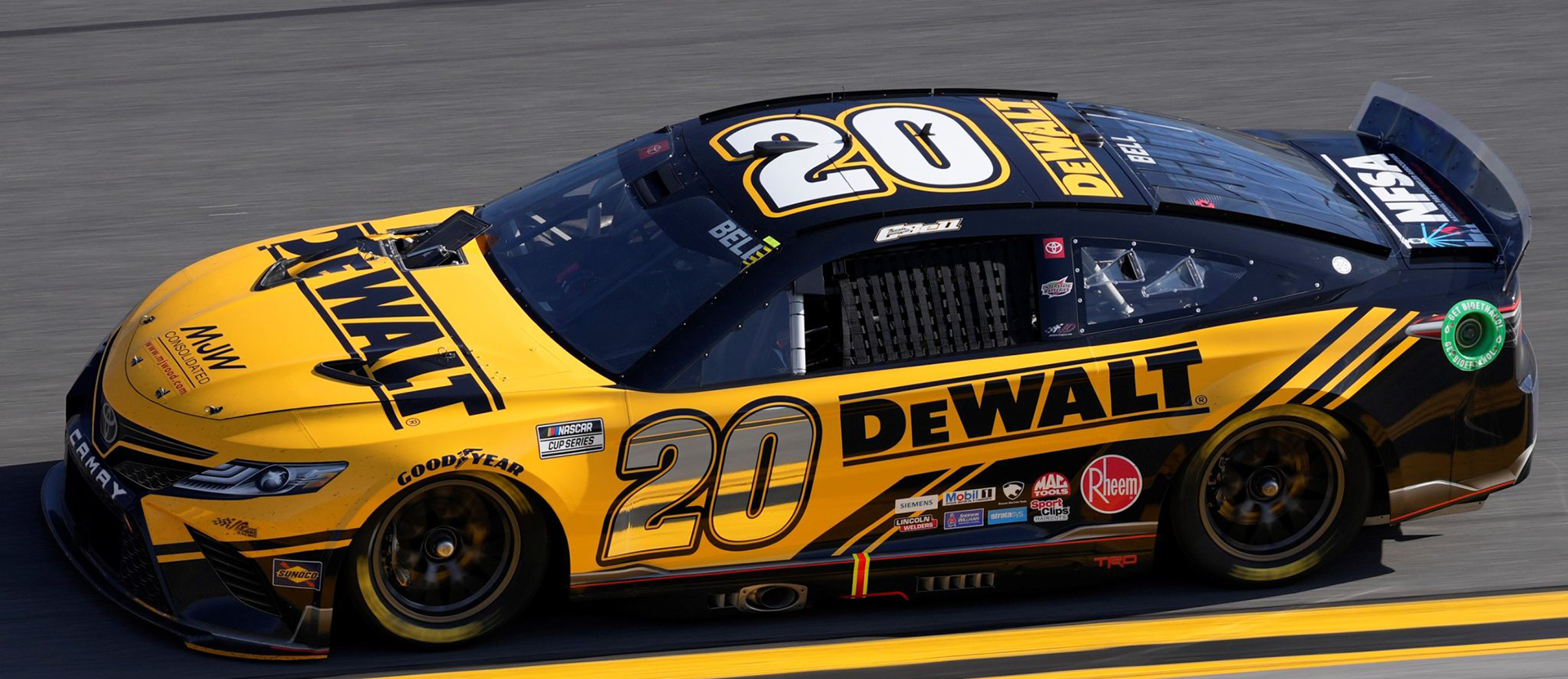
3D nyomtatás a NASCAR-ban
A motorsportot, ha nagy összességében nézzük, egyetlen cél hajtja: a lehető leggyorsabbnak és legmegbízhatóbbnak lenni, bármilyen lehetséges eszközzel. Az egyre bonyolultabb formák, a végtelenségig könnyített alkatrészek, a bővülő versenynaptárak okozta egyre feszesebb fejlesztési tempóval a már ismert gyártástechnológiák egyfajta gátat szabtak az autók külső és belső felépítésének, melyekbe a forradalmat a 3D nyomtatók hozták meg. De hogy működik ez egy olyan sportban, mint a NASCAR?
Miért épp a 3D nyomtatás?
A 3D nyomtatás több célt is szolgál a motorsportban. A prototípus- és járműtervezés első szakaszától a végleges alkatrészek gyártásáig mindenhol találkozhatunk vele. Akár a rég elfeledett autókat is visszahozhatja a versenypályára több évtized után!
A 3D nyomtatás, valamint a mechanikai szimulációk és a számítógéppel történő tervezőprogramok fejlődésével egyre összetettebb, már idehaza is ismert gyártástechnológiákkal nem megvalósítható alkatrészeket lehet létrehozni. Így drasztikus súlycsökkentést lehet elérni az autók össztömegében. Egy olyan kiélezett motorsportban, mint a NASCAR, ahol minden ezred másodperc számít, ez elengedhetetlen!
De mi az a 3D nyomtatás?
Kezdjük is egy gyors bemutatással. Mi is az a 3D nyomtatás?
A 3D nyomtatás lényege, hogy egy kiválasztott 3D modellt a kívánságainknak megfelelően beállítunk egy szoftverbe, ami az általunk meghatározott rétegekre bontja a formát. Egy 3D nyomtató ezeket a rétegeket helyezi egymásra, megalkotva az alkatrészt.
Rengeteg alapanyag áll rendelkezésünkre, hiszen betontól a fémeken át még csokit is nyomtathatunk! A legelterjedtebb nyomtatók mégis a műanyag nyomtatók. Ott pedig a határ a csillagos ég. És ezt a NASCAR is tudja.
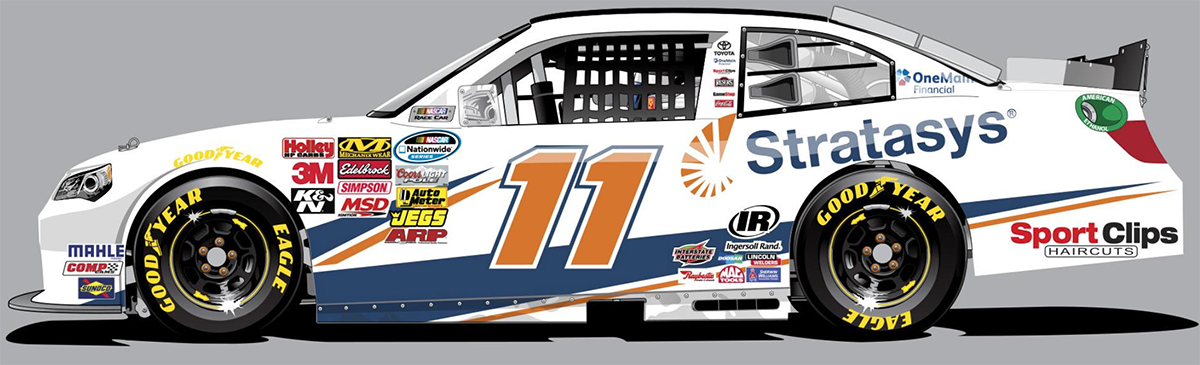
Az első nyomtatott alkatrészektől a Next Gen-ig
A sport első igazi úttörője a Joe Gibbs Racing volt. A JGR már 2004-ben partneri viszonyba lépett a világ legnagyobb gyártójával, a Stratasys-szal. Ekkor még egyszerűbb alkatrészek és szerszámok gyártására alkalmazták a technológiát, de készítettek analógóracsoport-tartókat és elektronikairendszer-dobozokat.
A partneri viszony még ma is aktív, a JGR, és azóta a Penske kiemelt technikai partnere a Stratasys. A Penske 2017 óta Stratasys gépekkel gyártja a 3D nyomtatott, autóba beépülő elemeiket. Egyik legjobb példa erre a 3D nyomtatott visszapillantótükör-tartójuk, melyet karbonszál erősített alapanyagból készítettek.
Felismerve a kapcsolat sikerességét, ma már nincs olyan NASCAR csapat, akinek a műhelyében ne lenne legalább egy 3D nyomtató. Még a Leavine Family Racing–nek is volt egy MakerBot nyomtatója, amivel karbon erősített alkatrészeket tudtak nyomtatni.
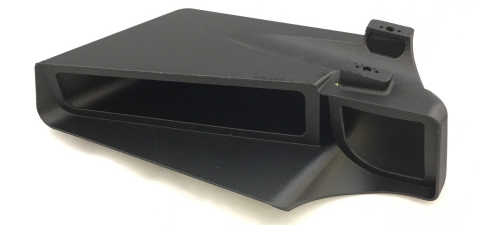
A Next Gen autók tervezésével és érkezésével a NASCAR felismerte, az új generációs autók egyenalkatrészei is lehetnek 3D nyomtatottak. Látván a JGR és a Penske egyértelmű sikereit, a NASCAR is a Stratasys mellett tette le a voksát. Az első prototípusok, és azok különböző verziói mind-mind 3D nyomtatással, vagy annak segítségével készültek, sőt, az első végleges Next GEN autók megjelenésükkor közel 30 különböző 3D nyomtatott egyenalkatrészt tartalmaztak és tartalmaznak a mai napig!
3D nyomtatott például az első szélvédő közepén található légbeömlő, a sofőr mögött és az autók alján található légbeömlők. Ezeket az egyenalkatrészeket a mai napig a NASCAR gyártja saját központjában!
A gyártók, hogy az autókat saját arcukra formálhassák, szintúgy rengeteg 3D nyomtatott prototípusalkatrészt használtak. A Chevrolet mérnökei a 2020-as Camaro ZL1 1LE aerodinamikai teljesítményét szélcsatorna-tesztekkel optimalizálták, és több mint 500 darab 3D nyomtatott prototípusalkatrészt teszteltek a karosszéria kifejlesztéséhez. Az autót 3D nyomtatott sebességváltó-hűtőcsatornával is felszerelték, amely 2020 végére már 27 versenyen, összesen 18 500 mérföldet tett meg.
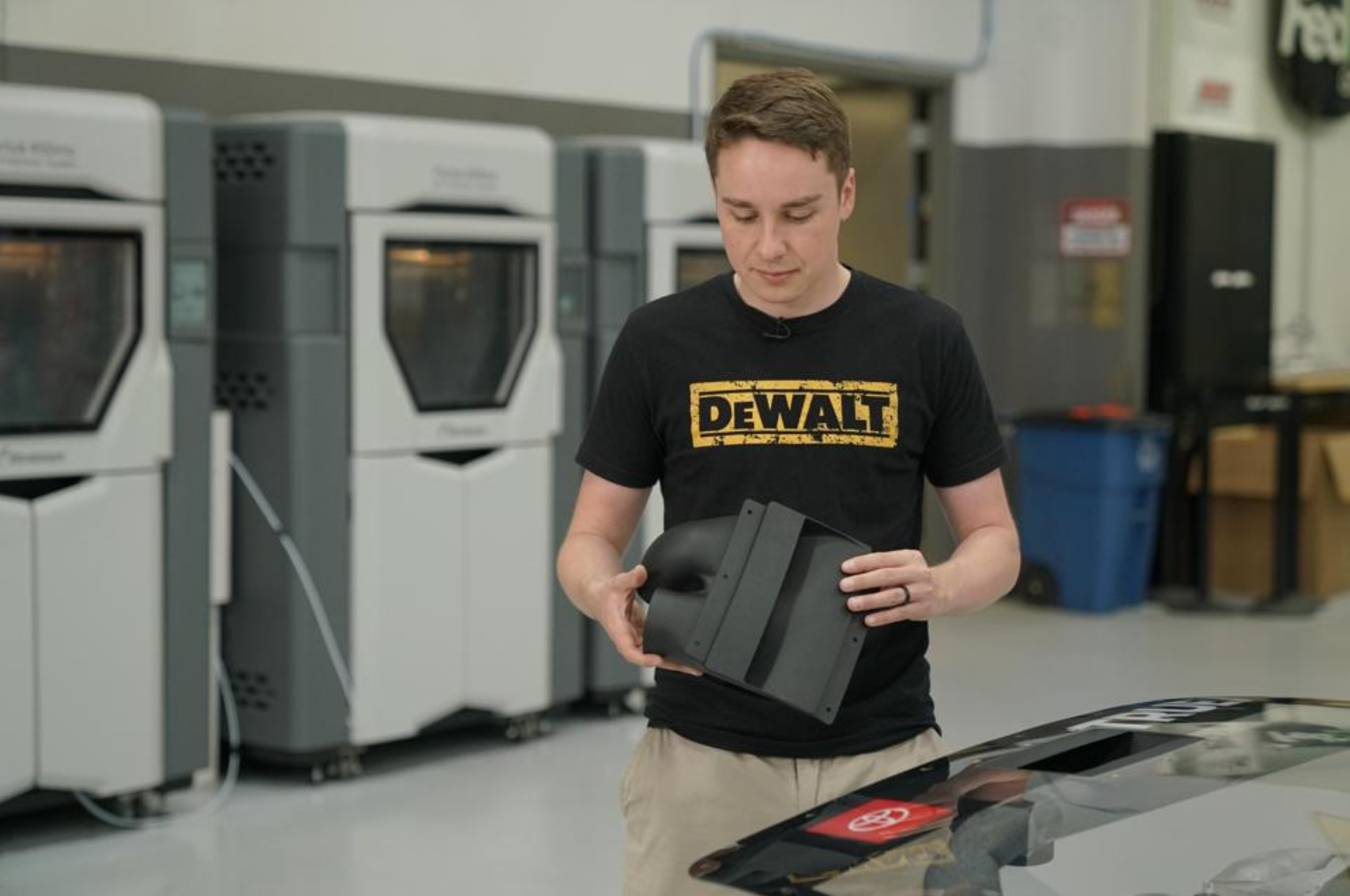
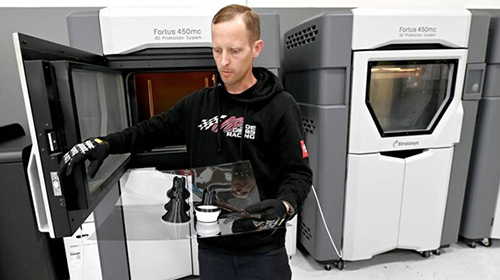
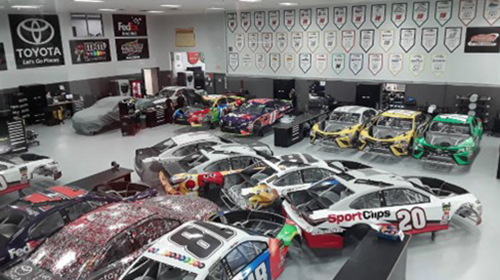
Mire jók ezek az alkatrészek?
Az elülső szélvédőn található nyílás ötlete 2021 szeptemberében született meg.
„A Daytona-ban tartott tesztelés során a versenyzők arról számoltak be, hogy a túl nagy meleg gondot jelentett az autó belsejében. A tesztelés idején a NASCAR aero-csapata azt találta ki, hogy szellőzőnyílásokat és csatornákat adnak hozzá az alulsó beömlőkhöz és a szélvédőhöz. Ez a légáramlás nagyjából 35-40 Fahrenheit (1,6-4,4 C) fokkal csökkentette a hőmérsékletet„ – mondta Brandon Thomas, a NASCAR Next Gen autótervezője és ügyvezető igazgatója.
A NASCAR számára a szélvédő légcsatornáit, amelyek segítenek a levegőt közvetlenül a pilótafülkébe vezetni, SAF porágyas technológiájú H350 nyomtatóval gyártotta a Stratasys. A NASCAR Concord-ban található kutatási és fejlesztési létesítményében Fortus 450mc 3D nyomtatókat is használnak a motorok hűtéséhez szükséges NACA aljzatcsatornák tervezéséhez és gyártásához.
De miért nem adják a csapatok kezébe a 3D nyomtatott alkatrészek gyártását?
Egyszerű, a csalás kizárása és a pilóták védelme miatt.
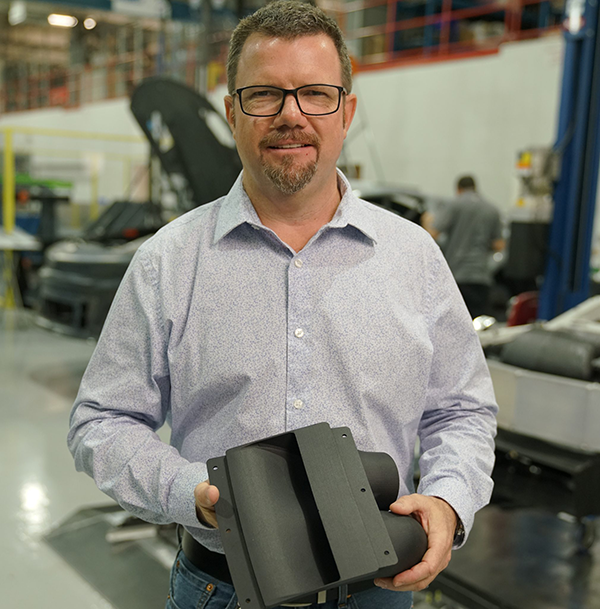

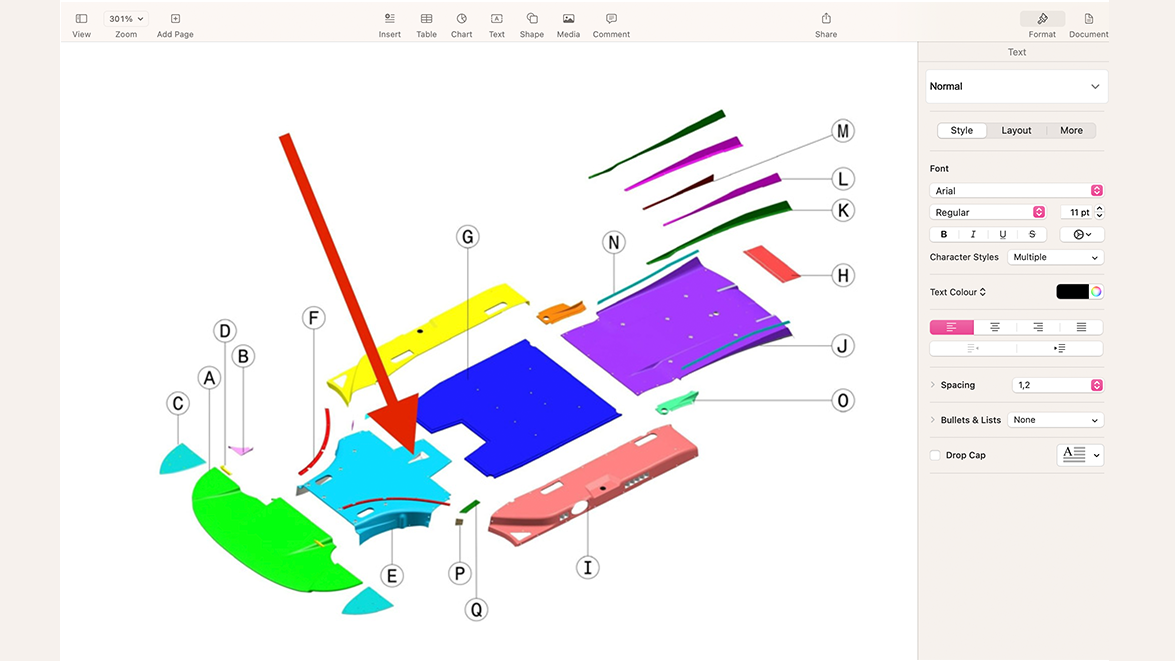
Hová tartunk?
Nehéz megmondani, mi lesz a következő nagy dolog, ami megváltoztatja a NASCAR-t és az autók felépítését. Ami biztos, hogy a csapatok és a tulajdonosok egyre többet invesztálnak a technológiába. A legjobb bizonyíték erre talán maga Brad Keselowski, aki több mint 10 millió dollárból létrehozta a Keselowski Advanced Manufacturing-et. Keselowski célja egy olyan cég létrehozása volt, ami a legmodernebb technológiákat összhangba hozva a legmagasabb minőségű fémalkatrészek gyártására hivatott. Gyártelepén belül a CNC megmunkálóközpont és a 3D nyomtató tökéletesen megfér egymás mellett, hisz a két technológia kiegészíti egymást.
Fémnyomtatott alkatrészeket pedig már korábbi generációkban is láthattunk. Az SHR például titániumból nyomtatott, radikálisan könnyített fékpedálokat használt már a GEN 6 autókban is. A fékpedál 32%-kal könnyebb lett, de 50%-kal erősebb is az eredeti pedálhoz képest.
Az alkatrészek és az autók fejlődése tehát egyértelmű. Természetesen a 3D nyomtatás nem csodaszer, ne várjuk azt, hogy kinyomtassanak egy teljes versenyautót. De abban biztosak lehetünk, hogy egyre több és több 3D nyomtatott alkatrész jelenik meg szeretett sportunk versenyautóiban.
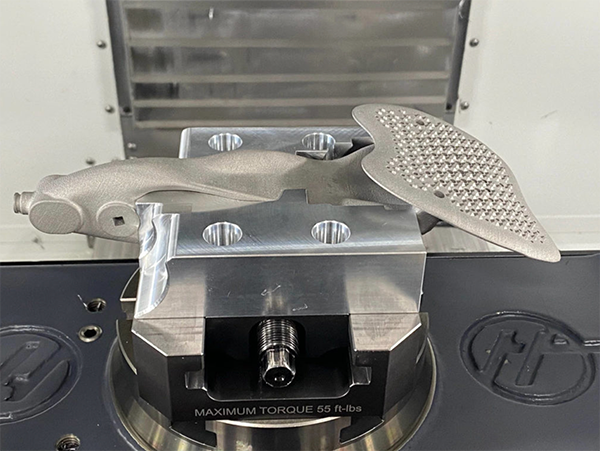
Az írás a Menjetek körbe! podcast, a Ground Effect és a Varinex Zrt. kooperációjában készült.
Tudta, hogy az additív gyártás legmegbízhatóbb és legnépszerűbb megoldása a Stratasys FDM technológia, és azon belül a karbonszállal erősített alapanyagok?
Tudta, hogy fém alkatrészeit is kiválthatja könnyű és extra-erős szénszálas kompozit 3D nyomtatott alkatrészekkel?
Ismerje meg a Stratasys megbízható kompozit 3D nyomtatóit a VARINEX csapatától!
25 éve segítjük additív gyártással Magyarország vezető ipari cégeit és innovációikat!