Additív Kapcsolatok
A vasárnapi húslevestől a szériagyártásig
Az okosabb autóhoz tehetségesebb emberek kellenek – ez a gondolat vezérli a Valeo vezetőit. A Valeo független ipari csoport, amelynek tevékenységi köre teljes egészében az autóiparra koncentrálódik. Autóipari beszállítóként valamennyi autógyár partnere világszerte, és veszprémi gyárában közel 2000 munkatársat foglalkoztat.
Ványi Zsolttal, a Valeo Auto-Electric Magyarország Kft. mintakészítési vezetőjével Bakonyi Csilla színész és kommunikációs szakember beszélget a 25 éves jubileum kapcsán.
A franciaországi központú Valeo magyarországi fejlesztő- és gyártásközpontjában a 3D nyomtatás a mindennapi munka részévé vált. Hogyan emlékszik vissza a kezdeti lépésekre?
2004-ben kerültem a Valeo-hoz, és 2007-ben vettem át ezt a területet. Az elején az elődöm, Jabronka László is ott dolgozott, én pedig még nem hivatalosan voltam mellette, akkoriban még nem volt közöm a 3D nyomtatáshoz, vagy bármilyen additív gyártáshoz.
Milyen területen dolgozott előtte?
A műanyag fröccsöntés és a gépészeti forgácsolás területéről jöttem, a Valeo is ebben a szektorban kezdett alkalmazni. Természetesen tudtam róla, hogy létezik 3D nyomtatás, de akkor még nem foglalkoztam ezzel komolyabban. A prototípusgyártás ad hoc jelleggel érkezett az életembe és megragadtam a lehetőséget, hogy cégen belül erre a szegmensre váltsak. Hirtelen ott találtam magam egy tárgyalóban az elődömmel, valamint Falk Györggyel és Jonathan Jaglommal. Rendkívül szkeptikusan figyeltem, ahogy egy kis alkatrész felett folyik a diskurzus, melynek minden paramétere szokatlan volt számomra.
A bérgyártás ennek ellenére elindult.
Igen, hisz kis csapattal, 6-7 emberrel indultunk, így rendszeresen kellett túlórázni, hogy teljesítsük a megrendelői igényeket. Épp egy Rolls-Royce alkatrészen dolgoztunk, amely egy dekorelem volt, ami elbírta, hogy ne legyen statikailag, strukturálisan olyan szilárd, mint amilyen a végső darab lesz. Sok mintát kértek tőlünk, Falk Györgyék pedig ezt legyártották nekünk. Ha szükség volt rá, akkor akár hétvégén is a rendelkezésünkre álltak. Így történhetett meg, hogy én egy vasárnapi húsleves után, családlátogatásból hazafelé tartva beugrottam Györgyhöz, ittunk egy kávét a teraszon és átvettem a megrendelt prototípusokat tartalmazó csomagot. Számtalanszor segítettek abban, hogy extra időn belül meglegyen a kért alkatrész. Innen indult a jó kapcsolat; nagyon rugalmasak voltak és nyilván látták a lehetőséget abban, hogy nyitottak vagyunk rá, hogy nagyobb darabszám, mennyiség esetén is használjuk ezt a technológiát.
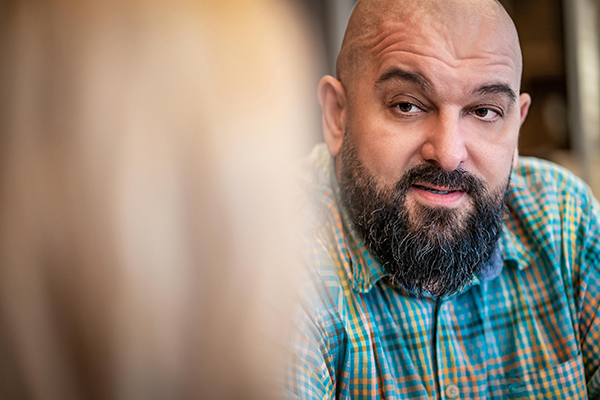
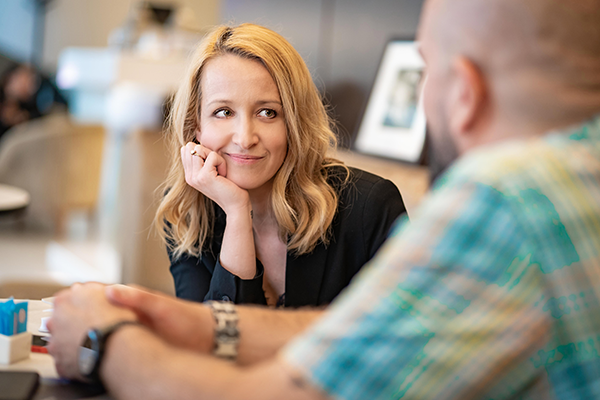
Mennyi idő kellett ahhoz, hogy ez a nyitottság ne csak egy szándék maradjon, sőt saját gép vásárlásában eszkalálódjon?
Valójában attól a naptól, hogy én gyanúsan nézegettem és méregettem az alkatrészeket, addig a napig, hogy elkezdtem harcolni azért, hogy vegyünk egy gépet Veszprémbe, maximum másfél év telt el. Amikor átvettem a műhelyt, elég kevés technológiánk volt, inkább csak egy gyártásindítás segítő protoműhely voltunk, amiből kinőttük magunkat azzá, akik vagyunk. Ebben a felívelő szakaszban jöttek olyan projektek, amikhez szükségünk volt a 3D nyomtatásra és olyan mennyiségben rendeltünk alkatrészeket a VARINEX-től, hogy nagyon hamar le tudtam vezetni a pénzügy felé: megéri beruházni saját 3D nyomtatóba. Ehhez kaptam persze segítséget, hiszen nagyon jó számítások álltak a rendelkezésemre a gyors megtérülésről, profittermelésről. Ezek a költségmegtérülési számítások olyan meggyőzőek voltak, hogy 2008-2009-ben már megvásároltuk az első, Eden 350 PolyJet gépünket. Mindenre is elkezdtük használni a 3D nyomtatási technológiát, meglehetősen kreatívan.
Mit jelent ez a kreativitás?
Egy másfajta szemléletet, hozzáállást. Fröccsöntőszerszám prototípus-gyártásra kezdtük el használni a forgácsolás helyett. Később mertünk kísérletezni empirikus úton, így olyan dolgokat is sikerült megcsinálnunk, amire azt mondták, hogy lehetetlen.
Miért volt erre szükség?
A munkánk kétharmad része validációs mintagyártás. Azt a designt, amit a tervező megálmodott, mi aszerint a feltételrendszer szerint teszteljük, amit majd a szériaterméken is végre kell hajtani. Ehhez az egyik feltétel, hogy olyan alapanyagból legyen a prototípus, mint a szériatermék, vagy a lehető legközelebb álljon hozzá. A PolyJet technológiánál nem azok az alapanyagok voltak, amiket mi használunk, ezért csak olyan alárendelt helyeken engedték meg a használatát, ahol nem volt funkciója. De természetesen egy rendkívül gyorsan fejlődő, innovatív iparágról van szó. Jelenleg két PolyJet nyomtatónk van. A már említett Eden 350, valamint egy Stratasys J750, amivel a több színű, többkomponensű alkatrészeket tudjuk gyártani. Ez sokszor rendkívül fontos, főleg dekorelemeknél. Ezen kívül volt egy projektünk az új DLP nyomtatóval, hisz ezzel a technológiával jó mechanikai és hőtűrésű anyagokat lehetne gyártani.
Mitől függ, hogy melyik technológiát alkalmazzák?
Mixeljük őket. Vagy a saját gépünket használjuk, vagy a VARINEX-től az SLS technológiát – mely bérgyártásban szokott a mai napig történni –, attól függően, hogy éppen az adott célra milyen technológiára van szükség. Mára a klasszikus mechanikus validáció jelentősége azonban csökkent az elektronikai-, valamint a hardver-és szoftverrendszerek validációs igényeinek megnövekedése miatt. 2004-ben még a VW Golf IV indexkar gyártása zajlott, amiben gyakorlatilag fém és réz alkatrészek voltak elektronika nélkül. Ehhez képest most a legújabb VW Golf VIII-ban egy több száz komponensből álló adat áramköri lap van és sokkal több hiba lehet abból, ha az elektronika vagy a hardver nem működik jól. Ezért a hangsúly áttevődött a hardver-és szoftverrendszer tesztekre.

Mi volt az a projekt, amire a legbüszkébb?
Volt komplett termékfejlesztésünk, volt, hogy egy hétvége alatt sikerült mintákat produkálnunk a BMW-nek, mellyel egy nem specifikált zaj problematikája megoldódott. A legbüszkébb mégis arra vagyok, ahogy növekedtünk az additív gyártás terén, és mára mi vagyunk az egyik legnagyobb, legkomplexebb mintakészítő műhely és tudásközpont a Valeo-n belül. Saját fejlődés volt, nem egy felülről vezérelt folyamat. A Valeo R&D területnél olyan szintű szakmai szabadság van, amivel sehol máshol nem találkoztam. Természetesen megvan az elvárás, mit szeretnének, megvan hozzá egy keretrendszer, de a megoldás rajtam múlik. Az egyik a másikat generálja. Ha van egy szabadság és egy elvárás, akkor fel fogsz nőni a feladathoz. Ha alkalmas vagy rá.
Ez nagyon motiváló tud lenni!
Hogyne! Ezt a hozzáállást képviselem a csapatomban dolgozó emberek felé is; mindenkit én vettem fel, az én szempontrendszerem szerint vannak ott.
Mik ezek a szempontok?
Legfontosabb, hogy milyen ember, illik-e a csapatba, milyen a hozzáállása. Cégen belül vettünk át egy kollégát, aki nem bízott a szakmai kvalitásaiban. Abban, hogy szakmailag fogja-e tudni azt, amit tudni kell. Mondtam, ne törődjön ezzel, ez a rész megtanulható, a személyiség és az attitűd nem. Én így dolgozom. Mindenkinek más a vezetői, szakmai preferenciája vagy szempontrendszere, de nekem ez mindig kifizetődő volt. Nincsen igazán példaképem, de Toto Wolff, a Mercedes Formula 1-es csapatának ügyvezető igazgatója kimondottan egy olyan légkört hoz létre, ahol ő nem akar érteni semmihez, viszont mindenkit hagy dolgozni; nincsenek bűnbakok, csak hiba van, amit meg kell oldani. Egy ilyen légkör kialakítása nekem nagyon szimpatikus, tehát próbálom ezt tenni. Működni látszik, mert elég önállóan dolgozik a csapatom. Ezt multi cégen belül is lehet csinálni, de ehhez az kell, hogy nekem is önállóságot hagyjon a menedzsment.
Van mód az évek alatt felhalmozott szakmai tudás továbbadására a közvetlen munkakörnyezetén túl?
“Expert” státuszban vagyok, tehát ha valakinek szakmai segítségre van szüksége, akkor megkereshet engem. Tartok tréningeket is, főleg Írországban és Csehországban. Az egyik tréningemre eljött egy kolléga olyan alkatrészekkel, amelyek nagyon ismerősek voltak. Kiderült, hogy fél évvel azelőtt videó- és telefonkonferencia keretén belül segítettem nekik, hogyan oldják meg a nyomtatott szerszámba fröccsöntött alkatrész problematikáját, és hozott nekem mutatóba egy darabot. Akkor éreztem, hogy ennek van értelme! Azt a tudást, amit mi összeszedtünk Veszprémben, egy kicsit tudtuk terjeszteni, megosztani egy cégen belüli másik területtel.
Vannak a technológiában kiaknázatlan területek?
Mi a gyártó része vagyunk a fejlesztő részlegnek. Szemléletváltásra van szükség. Ahhoz, hogy az a tervezésszabadság, amit ez a technológia tud nyújtani, ki legyen használva, a tervezők bevonása és támogatása feltétlenül szükséges. Kollégám, Kovács Zoltán főleg a technológia helyes tervezése területén segíti a tervezőket.
Helyes tervezéssel határ a csillagos ég? Van olyan szakmai vágya, ami megvalósításra vár?
Nagy mérföldkő lenne az első saját olyan szériagyártott termék, amelyben additívan gyártott alkatrész van.
Fotók: Gordon Eszter
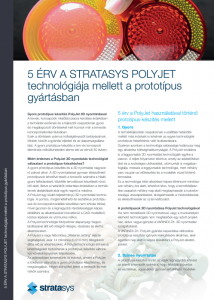