Additív kapcsolatok
„Ilyen dinamikusan változó világban elkerülhetetlen a 3D technológia használata”
A Procter & Gamble több mint három évtizede Magyarország egyik meghatározó nagyvállalata. Megbízható márkái (Ariel, Lenor, Pampers, Always, Braun, Gillette, Pantene) nemzedékek óta megtalálhatóak a háztartásokban.
Dobos Zsolttal, a P&G cserealkatrész-raktár vezetőjével beszélgettünk arról, hogyan segíti a munkáját a 3D technológia.
Hogyan indult a karrierje a Procter & Gamble-nél?
A ‘90-es évek végén Borsod megyében nem sok lehetősége volt egy huszonéves fiatalnak, így 1998-ban a párommal Budapestre költöztünk. Szerencsés voltam, mert rögtön a Hyginett Kft.-nél (Procter&Gamble/Hyginett Kft.) kezdtem dolgozni, akkoriban, mint gépbeállító technikus. A P&G-nek megvan az a jó tulajdonsága, hogy lentről neveli ki a vezetőit. Tehát nincs olyan, hogy például egy gyárigazgatót vesznek fel. Mindenkinek lentről kell kezdeni, és úgy küzdi fel magát az ember, kinek-kinek a maga karrierdöntése szerint. Én a magam részéről a technikai vezető szinten maradtam, és mint gépbeállító technikus 4-5 évig dolgoztam. Utána elkezdtem elindulni felfelé a ranglétrán, és most már tizenhatodik éve vagyok a cserealkatrész-raktár vezetője, valamint SAP key user lettem. Az SAP egy vállalatüzemeltetési szoftverrendszer, és nagyon komoly tudásra van szükség ahhoz, hogy valaki key user lehessen. Én az lettem, és elkezdtem oktatni is az embereket. Így most már a felnőttoktatástól kezdve, a 3D nyomtatáson át, egészen a cserealkatrész-raktár technikai vezetéséig, minden hozzám tartozik. Ez a technikai vezetés gyakorlatilag azt jelenti, hogy gondoskodnunk kell róla, hogy problémamentesen üzemeljen a raktár, legyenek mindig megfelelő alkatrészek, emel-lett minden SAP-val kapcsolatos ügyet én vezénylek le a gyáron belül.
Nem ambicionálta, hogy még feljebb lépjen azon a bizonyos ranglétrán?
Szeretem a munkámat. Szokták mondani, hogyha a hobbid a munkád, akkor szerencsés ember vagy, hiszen nem kell dolgoznod. Valahogy így vagyok ezzel én is. Kiváltképp az elmúlt 6-7 évben, mióta bejött a 3D nyomtatás az életünkbe. Most már a munkánk java részét ez teszi ki. De ez a rész egyre nagyobb lesz, mert mi is fejlődünk, és még tovább akarunk menni ezen az úton.
Hogyan indult el a cégnél a 3D nyomtatás?
Ha jól emlékszem, 2016 novemberében letettek a gyár a küszöbére egy 3D nyomtatót, egy Fortus 380-ast. Egy ifjú menedzser hölgy ötlete volt, hogy az egyik gyártósoron használható alkatrészt milyen remekül lehet majd ezzel gyártani. Egyébként nagyon drága alkatrészről volt szó, és kiszámolták, hogy tényleg gazdaságosabb a gyártása ezzel a technológiával. Szétnéztek a gyárban, hogy ki az, aki látott már 3D nyomtatót. Én akkor már évek óta foglalkoztam 3D nyomtatással hobbi szinten, így hozzám került a raktárba. Ez egy logikus döntés is volt egyben, hiszen cserealkatrészről volt szó, én pedig a cserealkatrész-raktár technikai vezetője voltam, vagyok. Nem telt sok időbe, hogy felismerjük a lehetőséget, ami ebben rejlik.
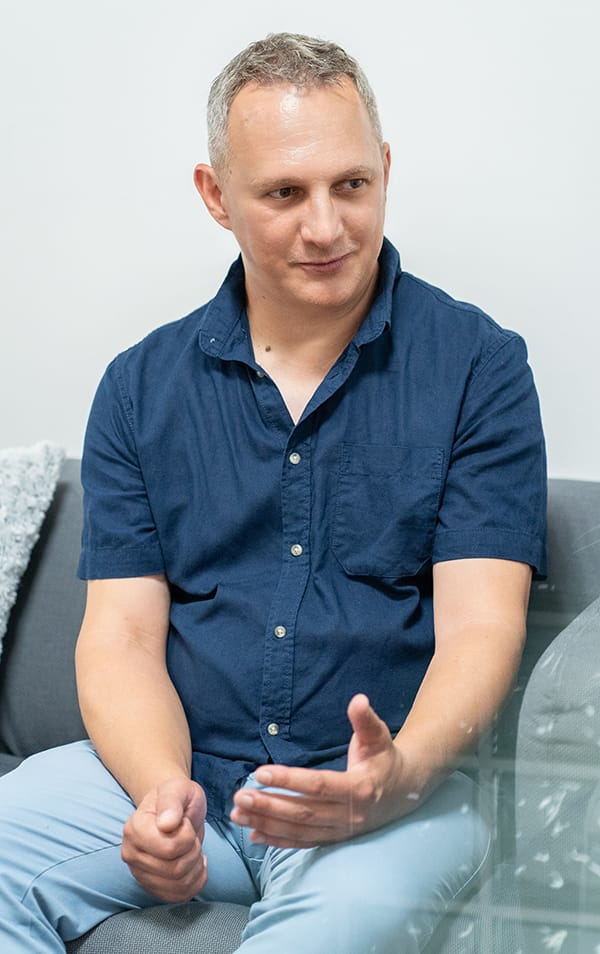
Sikerült legyártani azt az alkatrészt?
Konkrétan az a cél, amiért eredetileg megvették, nem jött össze, de ezer másiknál remekül működött. Két dolgot kell igazából megérteni ebben az egészben. Az egyik az az, hogy mi tisztasági betéteket, illetve tamponokat, intim higiéniai cikkeket gyártó cég vagyunk. Olyan gyártósorokkal gyártjuk ezeket a termékeket, ahol főleg mechanikai energiával vágjuk, gyűrjük, hegesztjük a termékeket. Ahhoz, hogy ez gazdaságos legyen, hogy ez megérje, nagyon nagy sebességgel kell gyártani a termékeket. Most pillanatnyilag a gyártósoraink 1500-2000 darab terméket gyártanak percenként. Ilyen teljesítmény mellett rendkívüli a mechanikai igénybevétel, és az alkatrészek kopnak.
A cserealkatrész-raktárban több mint 27 ezer féle alkatrészt tárolunk. Nem darab, 27 ezer féle! Ezeknek a nagy többsége egyedi gyártású – jórészt műanyag vagy alumínium – mechanikai alkatrész. Elkezdtük tesztelni a 3D nyomtatással készült, a Fortus 380-nal gyártott alkatrészeket. Kiderült, hogy a döntő többségénél kiválóan beválik. Nagyszerű minőségű az alapanyag, és nagyon erős alkatrészeket tud gyártani. Innen jött a következő lépés: kiszámoltuk, hogy mennyibe kerülne, hogyha megvennénk, illetve mennyibe kerül, hogyha előállítjuk az alkatrészt. Egyértelműen kijött, hogy még a legkevésbé “megérős” alkatrészeknél is a harmadába kerül, de általánosságban elmondható, hogy körülbelül 10 százaléka a beszerzési árnak. A másik fontos szempont, hogy fejlesztőgyár vagyunk. Bármi új dolgot találnak ki, és a sorokon fejlesztésre van szükség, azt nálunk kezdik el először kipróbálni. Hatalmas mennyiségű kísérleti alkatrészünk van. Ez megint csak egy döntő érv volt a 3D technológia mellett. Sokszor az eredetileg megtervezett alkatrész nem válik be, módosításokat kell rajta eszközölni. Néha csak egy furatot kell arrébb tenni, néha teljesen át kell tervezni az egész alkatrészt. Ezeknek az újratervezése is rengeteg idő, de az újragyártása főleg. Mivel legfőképpen japán, olasz, amerikai, kínai technológiákat használunk, könnyű kiszámolni: szállítási határidő, kommunikáció, vámok stb. Borzasztó drágává válnak így ezek a módosított alkatrészek. 3D nyomtató használatával viszont ez egyszerű: átküldik az újratervezett rajzot, mi pedig kinyomtatjuk. Nagyon gyorsan eljutottunk odáig, hogy az első nyomtató évente termelte ki az árát. Úgyhogy nem volt nehéz eldönteni, hogyan megyünk tovább.
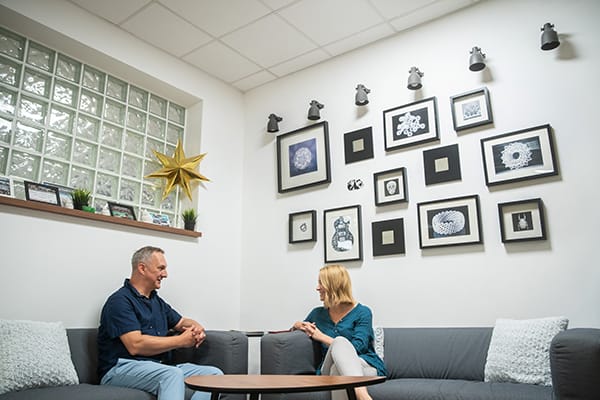
Ha Ön indítja el az első gépbeszerzési folyamatot, akkor mást választott volna?
Amikor 2016 novemberében ez a gép ott landolt a raktárban, bejöttek a VARINEX munkatársai, telepítették nekem a gépet, megtanítottak rá, hogyan kell használni, és elkezdtünk gyártani. Nem is volt más opció, mi már rögtön ezzel kezdtünk. Igazság szerint én az évek folyamán utánanéztem annak, hogy van-e egyáltalán a Stratasys-nak bármilyen versenytársa, de kiderült, hogy nincs. A Stratasys a maga kategóriájában világelső. Egyedülálló termékeket biztosít, és az alapanyagai is azok. Én, aki használok különböző típusú alapanyagokat otthon a hobbinyomtatásnál, nagyon hamar megtanultam, hogy nagyon nem mindegy, milyen alapanyaggal dolgozik az ember. A Stratasysban egyetlen egyszer sem kellett csalódni, mindig folyamatosan ugyanazt a minőséget tudja biztosítani.

Hobbi szinten mire használja leginkább a technológiát?
Filmes replikákat készítek. Ezekre egyrészt óriási kereslet van, tehát el is lehet adni őket, másrészt pedig gyűjtöm őket, tehát magamnak is gyártom őket. Korábban is csináltam replikákat, csak akkor még másfajta technológiákkal (műgyantaöntés, vákuumhúzás), de azoknak van egy határuk. 2010 környékén láttam egy YouTube videót arról, hogy milyen kísérletek vannak már a 3D nyomtatókkal. Akkor eldöntöttem, hogy nekem kell egy ilyen, és valamikor 2012 környékén megvettem az első nyomtatómat. Egy új univerzum nyílt ki előttem.
Ugyanez történt gyakorlatilag a 3D nyomtatás, mint ipari felhasználás területén is. Ahogy egyre inkább kerestük a lehetőségét annak, hogy hogyan lehet még jobban kiaknázni a benne rejlő potenciálokat, úgy jöttek elő az újabb és újabb ötletek. Aztán eljutottunk egy végpontig a Fortus 380-assal. Gyakorlatilag öt éve nem állt meg csak egy hosszú ünnepre, mert folyamatosan, megállás nélkül gyárt az a gép.
A megnövekedett igények miatt döntöttek az újabb gép vásárlása mellett?
2021-ben jutottunk el odáig, hogy jöhet a következő lépés. Akkor jött a Fortus 450-es az életünkbe a maga szénszálas műanyagával. Itt már egy kicsit könnyebben ment át a vásárlási folyamat, hiszen már-már várták.
Nem volt már a kezdeti szkepticizmus?
Nem! Nagyon hamar kiderült, hogy bizony a szénszálas műanyaggal, amit a Stratasys gyárt, nagyon sok alumínium és réz alkatrészt is ki lehet váltani. Gyakorlatilag egy törhetetlen műanyagról beszélünk, tehát az összes alumíniumtengelyt, -kart, ami méretben befér, le tudjunk gyártani és gyártjuk is azóta, megállás nélkül. 2022. július 1-én indítottuk el a tesztüzem után a gyártást a 450-es nyomtatónkkal, és gyakorlatilag idén május vége-június elejére már kitermelte az értékét. Ez önmagáért beszél. Eljutottunk arra a szintre, hogy most már nemcsak a gyár, de a teljes cégvezetés várja tőlünk a következő lépést. Itt jöttek képbe a fémnyomtatók: már szinte követelte a karbantartási részleg, hogy most már vasat is akarunk nyomtatni, kellenek a nyomtatott vasalkatrészek. Pillanatnyilag éppen megrendelés alatt van az első fémnyomtatónk, és a tervek szerint november elején rövid tesztüzem után el is kezdjük a sorozatgyártást. Ez nekem is egy új dolog lesz, ilyennel korábban én sem dolgoztam.

Terveznek még további nyomtatót, nyomtatókat vásárolni a meglévők mellé?
Én szívem szerint egy F900-as Stratasys gépet szerettem volna a következő lépésnek. Körülbelül egyéves folyamat nálunk egy ilyen drágább gép beruházásának a levezénylése. Rögtön azután, hogy üzembe helyeztük a fémnyomtatót, el is kezdjük a F900-as megvásárlását. Erre igény van a termelő karbantartási részlegek felől, mert a 900-as, méretéből fakadóan, óriási méretű alkatrészek gyártására alkalmas, és vannak óriási méretű alkatrészeink, amiket nagyon drágán vásárolunk meg. El lehet képzelni, hogy mire CNC technológiával kimarják, és mire végül megérkezik Japánból, Amerikából (vámmal, szállítási költséggel együtt) több ezer, néha tízezer dolláros tételről beszélünk.
Ami egyszer csak elkopik…
Nagyon gyorsan elkopnak! Mint már említettem, úgy számolunk, hogy körülbelül 10 százalék bekerülési költséggel fogjuk tudni előállítani ezeket az alkatrészeket. Az ezzel nyert összegek mind-mind a vállalat megtakarításait fogják bővíteni, növelni.

Milyen az együttműködésük a VARINEX Zrt.-vel?
Kiváló partnerre találtunk a VARINEX-ben! Nagyon eredményes az együttműködésünk, mint szolgáltatóval és mint forgalmazóval, már-már baráti. Mindig tudják, hogy mit akarunk, és mindent megtesznek azért, hogy minél előbb összejöjjenek az üzletek. A fémnyomtató beszerzése is rövidebb volt velük, mint lett volna egy másik céggel, akik nem így állnak hozzá, hozzánk. Én nagyon boldog vagyok, hogy egy ilyen csapattal találkoztam.
A bérnyomtatást is igénybe kell venniük, vagy a két meglévő gép kiszolgálja az igényeket?
Műanyag alkatrészeket tekintve kiszolgálja, de éppen most bérnyomtatásban rendeltem fémalkatrészt, mert nagyon gyorsan szükség volt rá. De valójában az elmúlt öt évben nem volt rá példa, hogy a bérnyomtatást igénybe vettük volna. Ellenben hatalmas mennyiségű alapanyagot rendelünk folyamatosan.
Mit mondana azoknak, akik még hezitálnak a 3D nyomtatással kapcsolatban?
Ennyi év tapasztalat után az ipari 3D nyomtatás területén elmondhatom, és mindig mondom is, hogy nem az a kérdés, hogy kell-e ez nekünk. Nem az a kérdés, hogy van-e erre pénzünk. Ez kötelező! Ezt a technológiát be kell vezetnie minden olyan ipari cégnek, amely nagy mennyiségben állít elő akár egyedi gyártású, akár sorozatgyártású alkatrészeket. Az alkatrész előállítási költsége elképesztő mértékben csökken. Van erre egy példám, már több helyen elmondtam, hogy ha van az embernek egy olyan bróker ismerőse, aki a nehezen megkuporgatott 50 millió forintját elkéri, és egy év múlva visszaadja, és egy év múlva megint visszaadja, és egy év múlva megint, akkor azt a brókert megbecsüljük. Ilyen a VARINEX, ők így működnek, hogy gyakorlatilag az általuk forgalmazott gépek évente kitermelik az értéküket. Ehhez nyilván szükség van egy csapatra, akik kellőképpen támogatják ezt. A mi esetünkben ez a karbantartási csapat volt, akik a gyárban található, több mint 40 gyártósornak a karbantartásáért felelnek, és napi szinten tonnaszám építik be az új alkatrészeket, amik elkopnak. Kell az ő támogatásuk, akik kifejezetten akarják, hogy az alkatrészek ezzel a technológiával készüljenek, és kell nyilván egy hozzám hasonló ember, aki ezt az egészet intézi is nekik. Egy nagyon jól kidolgozott rendszert találtunk ki erre a cégünknél. Gördülékenyen működnek a gyártások, rendelések cégen belül, és minimális energia- és anyagköltséggel számolunk csak az alkatrészek áránál.
Ezt a kidolgozott rendszert egyedül működteti, vagy van egy csapata?
Pillanatnyilag én csinálom egyedül. Nem tudom, hogy pontosan hogyan fog alakulni a jövő, de a jelenlegi terveink szerint idővel bővíteni fogjuk ezt az egészet, úgyhogy muszáj lesz bővíteni a személyzetet is, akik ezzel foglalkoznak. De egy könnyen megtanulható, egyszerű technológiáról van szó. Ilyen dinamikusan változó világban egész egyszerűen elkerülhetetlen ennek a technológiának a használata. Egyfajta önfenntartásról lehet beszélni már a 3D nyomtatásban. Az olyan cégek, mint amilyen a miénk is, már nem a beszállítókra hagyatkozva próbálják megoldani a problémáikat, hanem előre gondolkodnak, és az önfenntartás irányába mennek el. Ez egy remek irány, minden erővel támogatni kell. Ez nem a jövő, ezt kell megérteni. Ez már a jelen, ebben már benne vagyunk. A kérdés csak az, hogy miért nem használja mindenki.
Ön szerint hol van ennek a technológiának határa?
Amilyen ütemben fejlődik ez a technológia évről évre, ezt nagyon nehéz lenne megjósolni. Ami tíz éve elképzelhetetlen volt, az már itt van. Vegyünk egy egyszerű példát: egy vastömböt, amiben egy íves furat van, semmilyen módon nem lehet legyártani, mert nem lehet ívben fúrni a vasba. Viszont 3D nyomtatással ez már kivitelezhető. Ez alapvetően értelmezi át az alkatrésztervezések folyamatát, új irányt mutat. Mert a tervező képes lenne megtervezni egészen elképesztő formájú alkatrészeket is, amelyek anyag- és energiatakarékosak és jobb mechanikai képességgel bírnak, de ki az, aki legyártaná hagyományos eszközökkel? Nincs rá mód. A 3D technológiával viszont ez megoldható, csak a kreativitás – vagy annak hiánya – szabhat határt.

Az interjút Bakonyi Csilla színész, kommunikációs szakember készítette.
Fotók: Gordon Eszter

A Continental is Stratasys FDM additív gyártással erősíti a termelési képességeit
A Continental AG, az autóipari technológiák egyik meghatározó vállalata már több, mint 20 éve sikerrel alkalmazza az additív gyártást. A németországi Karbenben található Additív Design és Gyártási Kompetencia Központja a teljes tervezési és a gyártási folyamatába integrálja a technológiát.
Kíváncsi rá, hogyan illesztette be a Continental gyártási folyamataiba a Stratasys Fortus 450mc 3D nyomtatót? Töltse le 4 oldalas, magyar nyelvű esettanulmányunkat!
