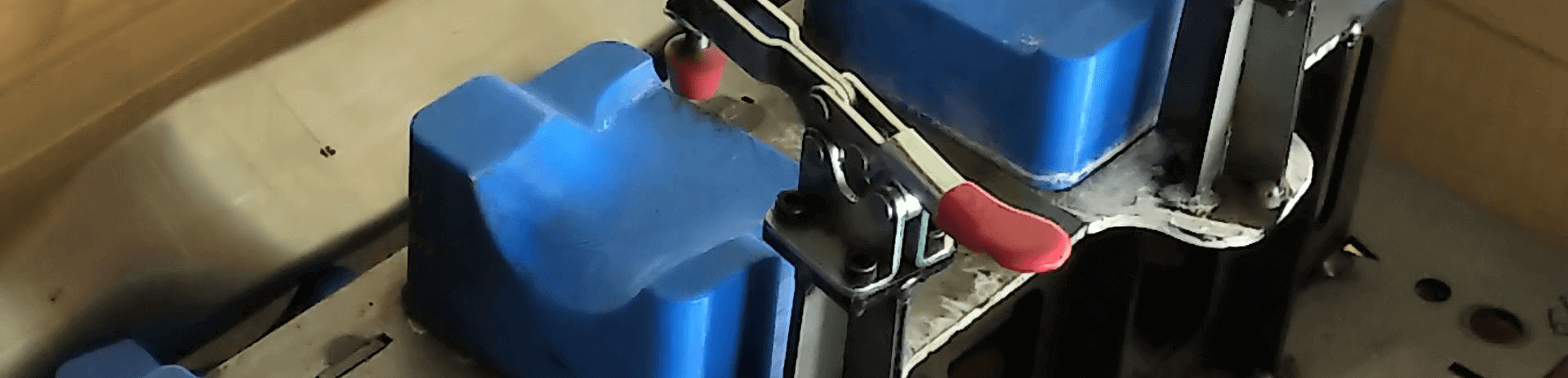
Gyártósori befogó készülékek additív gyártással - Mawe Presstec esettanulmány
A fémlemezgyártás területén 30 éves tapasztalattal rendelkező német Mawe Presstec GmbH egyedi megoldásokat kínál olyan kulcsfontosságú ágazatok számára, mint a repülőgépipar, az autóipar, az orvostechnikai eszközök gyártása, a gépészet és az építőipar. A kiváló minőségű – gyakran személyre szabott – termékek gyártásához elengedhetetlenek a különböző gépekhez és gyártási folyamatokhoz való egyedi szerszámok és befogó készülékek.
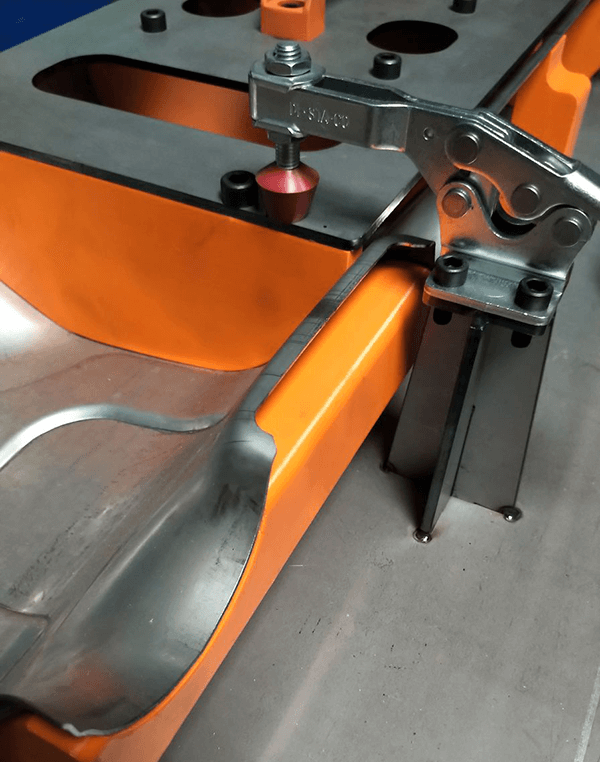
A gyártóüzem átalakítása
A Mawe Presstec felismerte, hogy a jellemzően különböző fémekből, például alumíniumból készülő szerszámok és szerelvények előállítása, újrarendelése vagy cseréje időigényes és költséges. Ez arra késztette a vállalatot, hogy felkutassa a helyettesítésre szolgáló gyártási technológiákat. Az additív gyártás által kínált előnyök tudatában Marco Werling ügyvezető igazgató kezdeményezésére egy Stratasys F170™ ipari 3D nyomtatóba ruháztak be, hogy házon belül gyárthassák az egyedi befogó készülékeket és szerszámokat.
Az eredmények – magyarázta Werling – megdöbbentőek voltak. A Mawe Presstec jelentősen lerövidítette a fejlesztési ciklusokat és folyamatokat a gyártósori gépekhez való befogó készülékek és szerszámok 3D nyomtatással, hőre lágyuló műanyagokból történő gyártásával.
„A Stratasys F170 rendszerrel történő additív gyártás csökkentette az alkatrészek előállítási idejét, és racionalizálta a teljes fejlesztési folyamatot gyárunkban” – mondta az ügyvezető. „A korszerű hőre lágyuló műanyagból készülő befogó készülékek gyártása óriási időmegtakarítást eredményez számunkra – bizonyos alkatrészek esetében akár 50%-ot is -, mindeközben magasabb fokú testreszabhatóságot és rugalmasságot is biztosít. Az F170 a nap 24 órájában képes működni – ez nagyobb termelékenységet és nonstop nyomtatási kapacitást jelent.”
A Mawe Presstec fémlemez megmunkálási projektjei gyakran igényelnek egyedi befogó készülékeket bizonyos geometriák és formatervek eléréséhez. Ezeket az eszközöket rendszeresen frissíteni kell, hogy megfeleljenek az adott munka követelményeinek. Jó példa erre az egyik olyan gyártósori befogó készülék, amelyet módosítani kellett a csuklópántok befogásához. Ezt általában több lépésben gyártanák vagy külső forrásból szereznék be, de a Mawe Presstec az F170-es gépen képes volt a zsanérokkal ellátott rögzítést egyetlen nyomtatási műveletben elkészíteni.
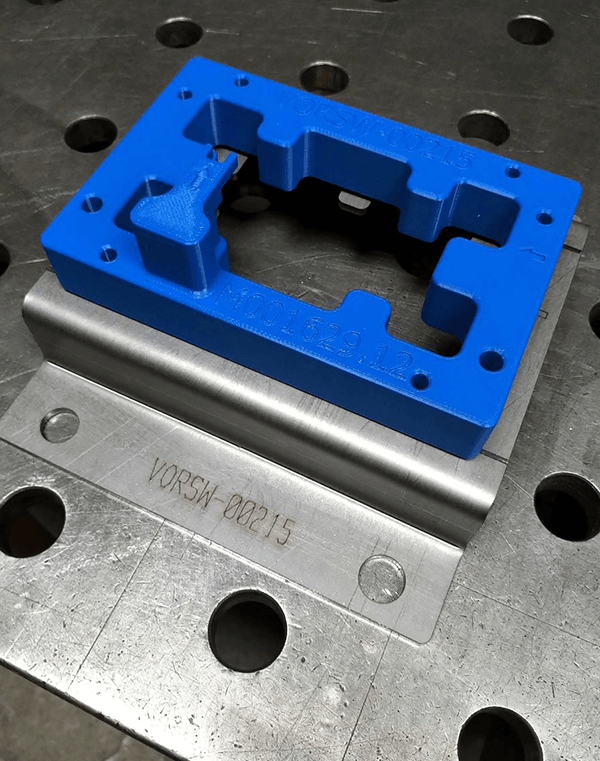
A befogó készülékek gyártási költségének csökkentése
A Stratasys F170 a telepítése óta jelentős időmegtakarítást eredményezett, és segített elérni a Mawe Presstec célkitűzését is, hogy csökkentse a gyártási költségeket. A fémből készült gyártósori befogó készülékek és szerszámok helyettesítése additív gyártású alternatívákkal csökkentette az alkatrészenkénti költséget, és a lemezalkatrészek kezeléséhez is hasznos megoldásnak bizonyult.
„20-30%-os költségmegtakarítást érünk el alkatrészenként, pusztán azzal, hogy az anyagköltségek csökkentek a korábban a befogó készülékek gyártásához használt fémhez képest” – mondta Werling. „Az additív gyártással az anyagpazarlást is csökkentjük.”
A Mawe Presstec a nyomtatási feladataihoz a mérnöki ABS alapanyagot választotta, amely megfelel a befogó készülék-gyártás összes kritériumának. Ezek az eszközök nagyfokú tartósságot és ütésállóságot igényelnek, hogy ellenálljanak a gyártási folyamat során rájuk ható erőknek. Ugyanakkor hőállóságra és geometriai pontosságra is szükség van a gyártóeszközök hatékony működéséhez.
Az FDM ABS tulajdonságai további előnyöket biztosítanak a polírozott fémtermékekkel érintkező befogó készülékek esetében. A gyártás hajlítási és alakítási szakaszaiban a fémből készülő befogók megkarcolnák a termékek polírozott felületét. Az ABS merevség-lágyság aránya azonban kiküszöböli ezt a problémát. Ezenkívül a GrabCAD Print™ Advanced FDM segédprogramjának használatával a gyártósori befogó készülékek úgy nyomtathatók ki, hogy a munkadarabbal érintkező felületeken ne legyenek varratok, így biztosítva a sima, karcmentes felületet.
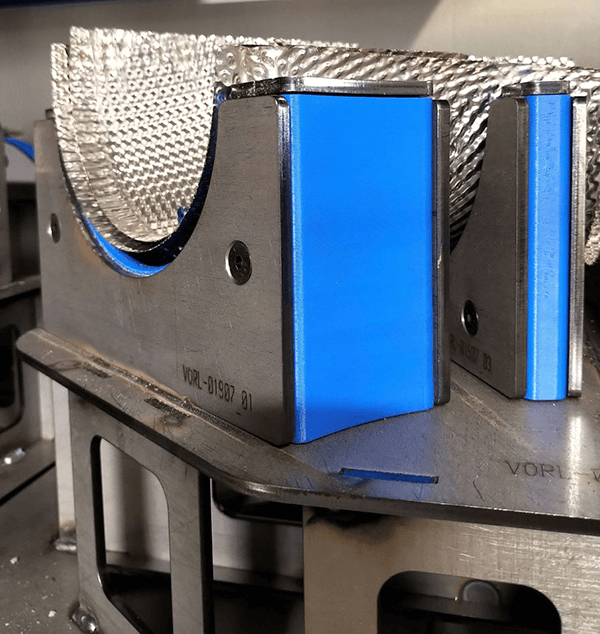
A tervezési ciklus felgyorsítása 3D nyomtatással
Az FDM ABS hőre lágyuló műanyag sikeres alkalmazásán túl a Mawe Presstec az F170 3D nyomtató használatát kiterjesztette a prototípusgyártásra is. Mint Werling kifejtette, ez jelentősen hozzájárult ahhoz, hogy a termékprototípusok segítségével könnyebben láthatóvá tegyék a formaterveket a potenciális és a meglévő ügyfelek számára. A bonyolult tervezési igényeket sokkal gyorsabb egy fizikai prototípus segítségével elemezni és megoldani, és felgyorsul a teljes értékesítési folyamat.
„Az F170 pozitív hatással volt a szolgáltatásainkra, mivel a 3D nyomtatott prototípusokat hatékonyan tudjuk használni az értékesítési megbeszéléseken és a tervellenőrzésben” – tette hozzá Werling. „Egy másik nagyszerű eszköz a terméktervezési ciklus lerövidítésében a GrabCAD Print szoftver, amellyel gyorsan és egyszerűen küldhetjük a CAD-fájlokat a 3D nyomtatóra. A GrabCAD szoftver sokkal kényelmesebbé és egyszerűbbé tette a házon belüli gyártásunk tervezési szakaszát.”
A Mawe Presstec zökkenőmentesen integrálta a Stratasys F170 3D nyomtatót a szerszámok és gyártósori befogó készülékek gyártásába, valamint a vállalkozás prototípusgyártási követelményeibe. A berendezés értékes kiegészítője a gépparknak, bővíti a cég gyártási képességeit, és lehetővé teszi, hogy a Mawe Presstec szakemberei a lényegre összpontosítsanak: a lehető legjobb lemezipari termékek előállítására az ügyfelek számára.
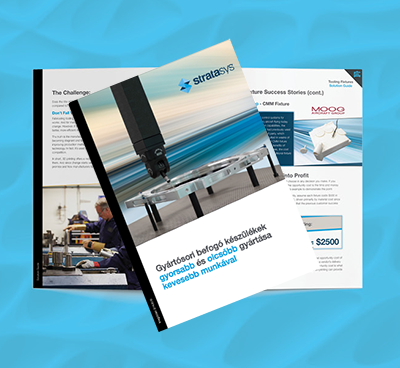
Ismerje meg, hogyan hozhat az additív gyártás új lendületet a befogó készülékek gyártási folyamatába, miközben növeli az idő- és költségmegtakarítást!
Töltse le 12 oldalas, magyar nyelvű,
GYÁRTÓSORI BEFOGÓ KÉSZÜLÉKEK GYORSABB ÉS OLCSÓBB GYÁRTÁSA
című megoldási útmutatót!